Conveyor systems are an integral part of many industries, providing a means for the seamless movement of materials and products. Round link steel chains are commonly used in horizontal, inclined, and vertical conveyor systems, providing the necessary strength and durability to withstand the rigors of continuous operation. In this blog, we will explore the importance of chain wear resistance in conveyor systems and the key factors that contribute to it.
SCIC round link steel chains are manufactured with CrNi alloy steel, known for its excellent tensile strength and anti-corrosion properties. The chains undergo a carburizing process to enhance their surface hardness, with a target range of 57-63 HRC (Rockwell hardness scale). This high level of hardness ensures that the chains can withstand the abrasive forces and wear associated with conveying heavy loads over extended periods.
In addition to surface hardness, the core area hardness of the chains is also crucial in determining their overall wear resistance. SCIC chains are engineered to have a core area hardness of 40-45 HRC, striking the right balance between toughness and hardness. This combination of hardness properties allows the chains to resist deformation and maintain their structural integrity under varying loads and operating conditions.
The carburizing depth of the chains is another critical factor that influences their wear resistance. SCIC chains are designed to have a carburizing depth of up to 2.5mm, ensuring that the hardened layer extends deep into the material. This depth contributes to the overall durability of the chains, providing a protective barrier against wear and extending their service life.
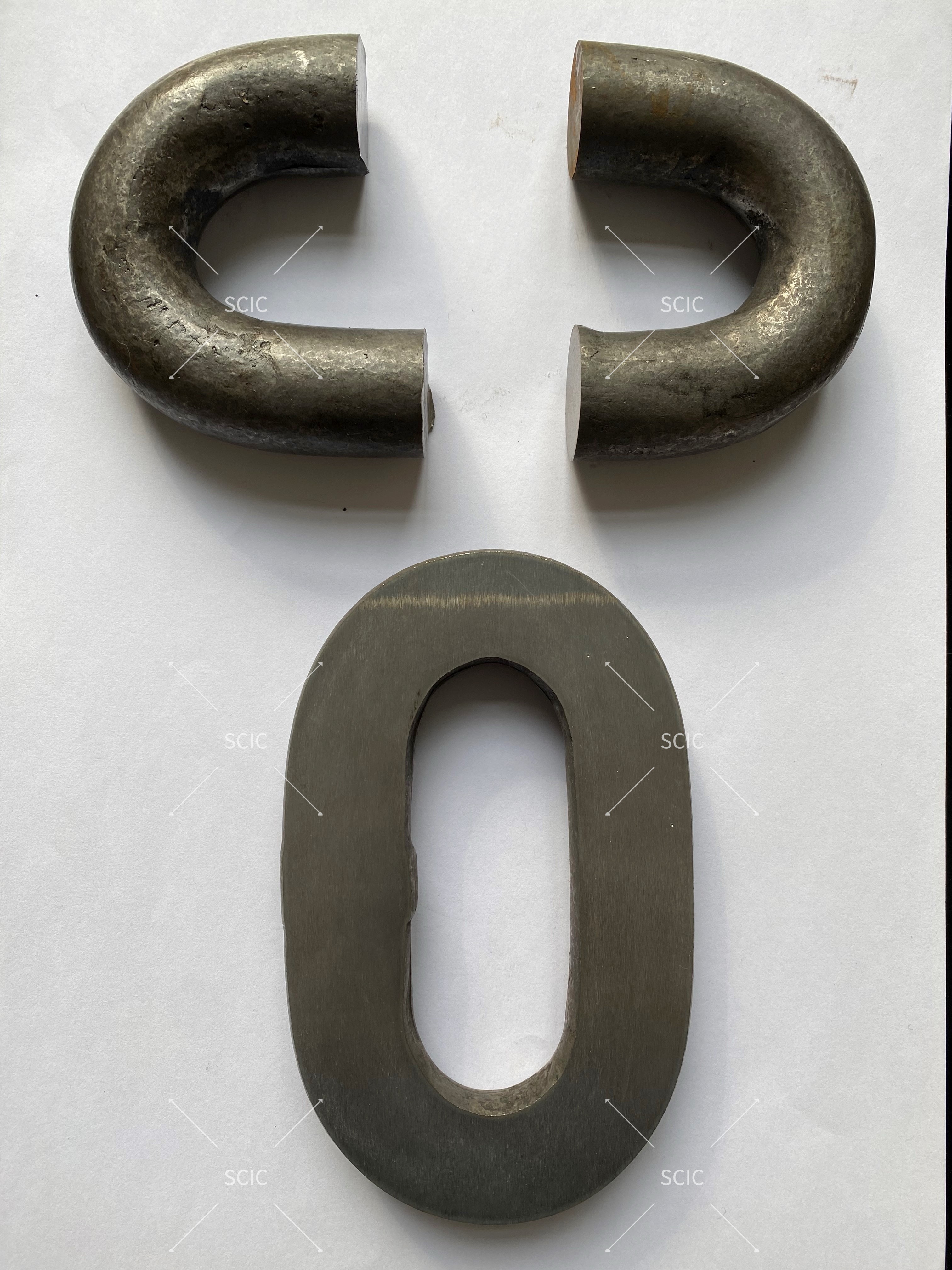
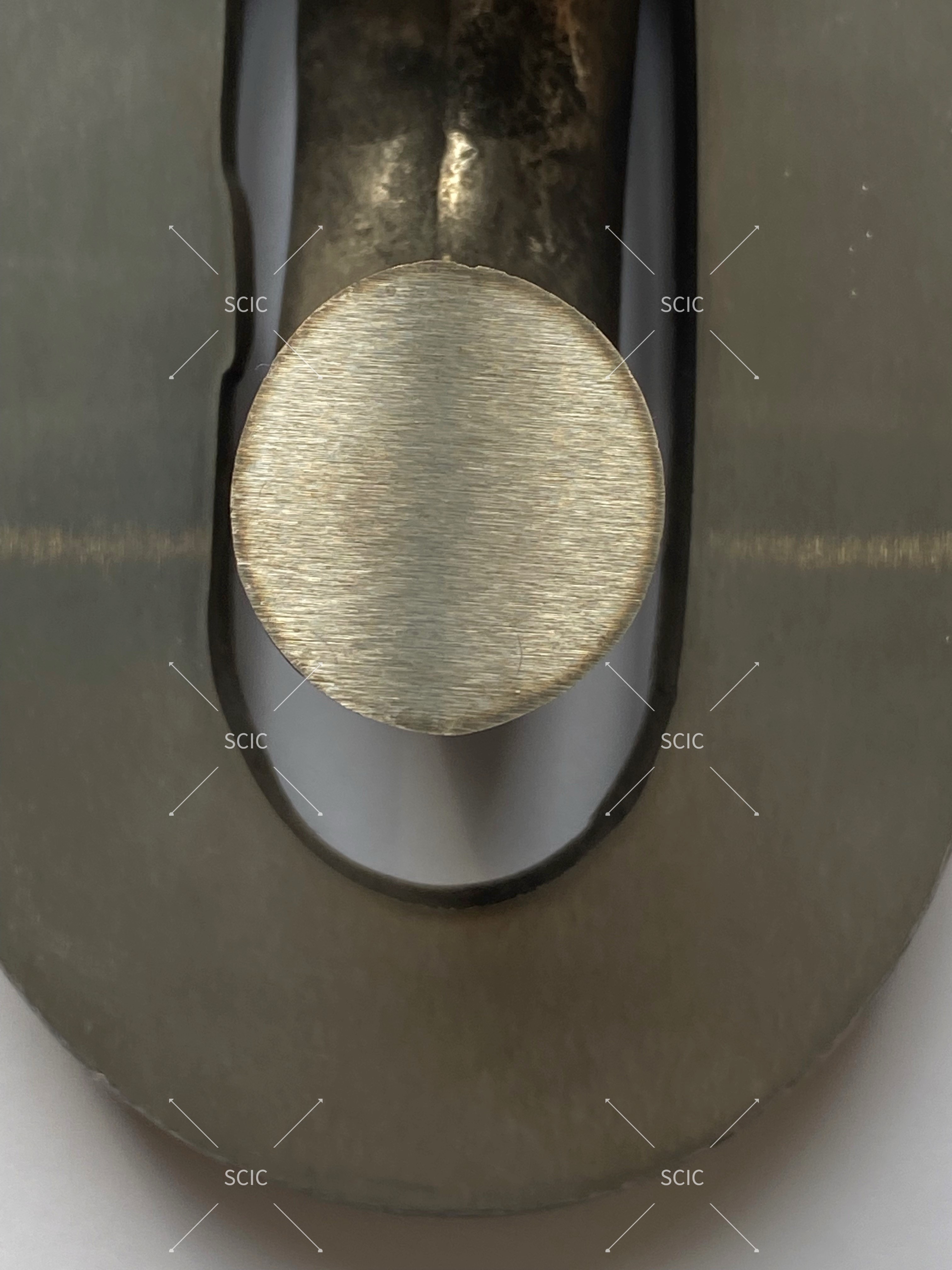
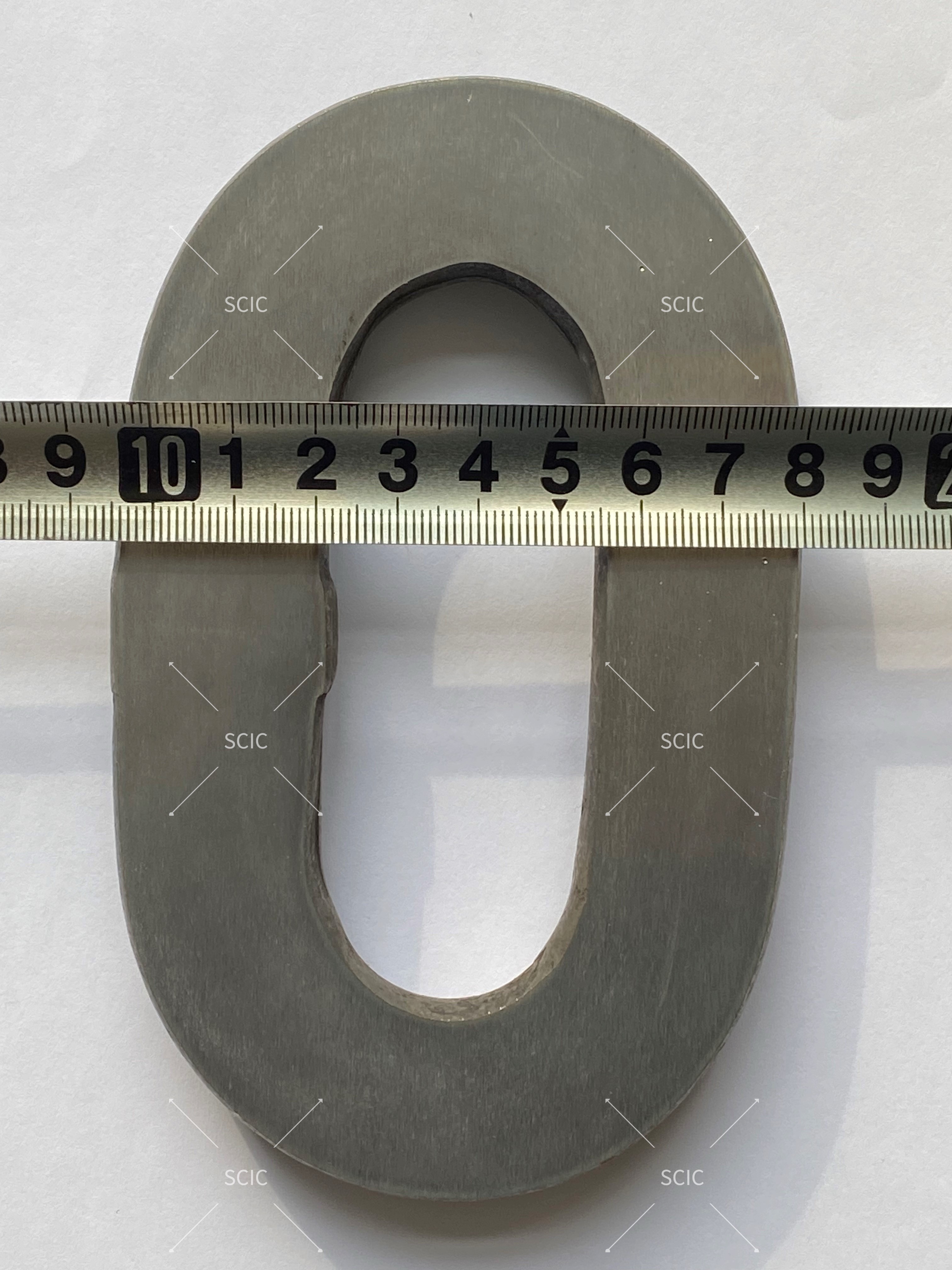
To validate the hardness and wear resistance of the chains, rigorous testing is conducted to measure their properties. A chain hardness test report is generated, detailing the specific parameters such as surface hardness, core area hardness, and carburizing depth. This comprehensive assessment provides assurance of the chains' quality and performance, giving customers confidence in their reliability for demanding applications.
In addition to the material and heat treatment, the design and construction of the chains play a significant role in their wear resistance. Highly calibrated chain strands are employed, ensuring that each link meets stringent specifications for dimensional accuracy and consistency. This precision manufacturing results in more accurate chain properties, particularly beneficial for multi-strand applications where uniformity is essential for smooth operation.
The optimized running geometry of the chains, in conjunction with compatible components and wheels, further enhances their wear resistance. The interlink contact is carefully engineered to minimize friction and wear, promoting efficient power transmission and reducing the risk of premature failure. This attention to detail in the chain's design contributes to its overall longevity and reliability in conveyor systems.
SCIC round link steel chains for conveyor systems are available in various sizes, including 16 x 64mm, 18 x 64mm, 22 x 86mm, 26 x 92mm, and 30 x 108mm, catering to a wide range of conveyor system requirements. Whether used in mining, cement, steel, or other heavy-duty industries, these chains deliver exceptional wear resistance and performance, ensuring uninterrupted material handling operations.
The wear resistance of round link steel chains is a pivotal aspect of their suitability for conveyor systems. By incorporating high surface hardness, core area hardness, and carburizing depth, along with meticulous design and testing, SCIC chains offer exceptional durability and reliability in demanding applications. When paired with proper maintenance and lubrication, these chains can contribute to the seamless and efficient functioning of conveyor systems, ultimately benefiting the productivity and profitability of industrial operations.
Post time: Feb-28-2024