For round link chains used in slag scraper conveyors, the steel materials must possess exceptional strength, wear resistance, and the ability to withstand high temperatures and abrasive environments.
Both 17CrNiMo6 and 23MnNiMoCr54 are high-quality alloy steels commonly used for heavy-duty applications like round link chains in slag scraper conveyors. These steels are known for their excellent hardness, toughness, and wear resistance, especially when subjected to case hardening by carburizing. Below is a detailed guide on heat treatment and carburizing for these materials:
Hardness testing is a critical step in ensuring the quality and performance of round link chains made from materials like 17CrNiMo6 and 23MnNiMoCr54, especially after carburizing and heat treatment. Below is a comprehensive guide and recommendations for round link chain hardness testing:
2. Vickers Hardness Test (HV)
- Purpose: Measures hardness at specific points, including the case and core.
- Scale: Vickers hardness (HV).
- Procedure:
- A diamond pyramid indenter is pressed into the material.
- The diagonal length of the indentation is measured and converted to hardness.
- Applications:
- Suitable for measuring hardness gradients from the surface to the core.
- Equipment: Vickers hardness tester.
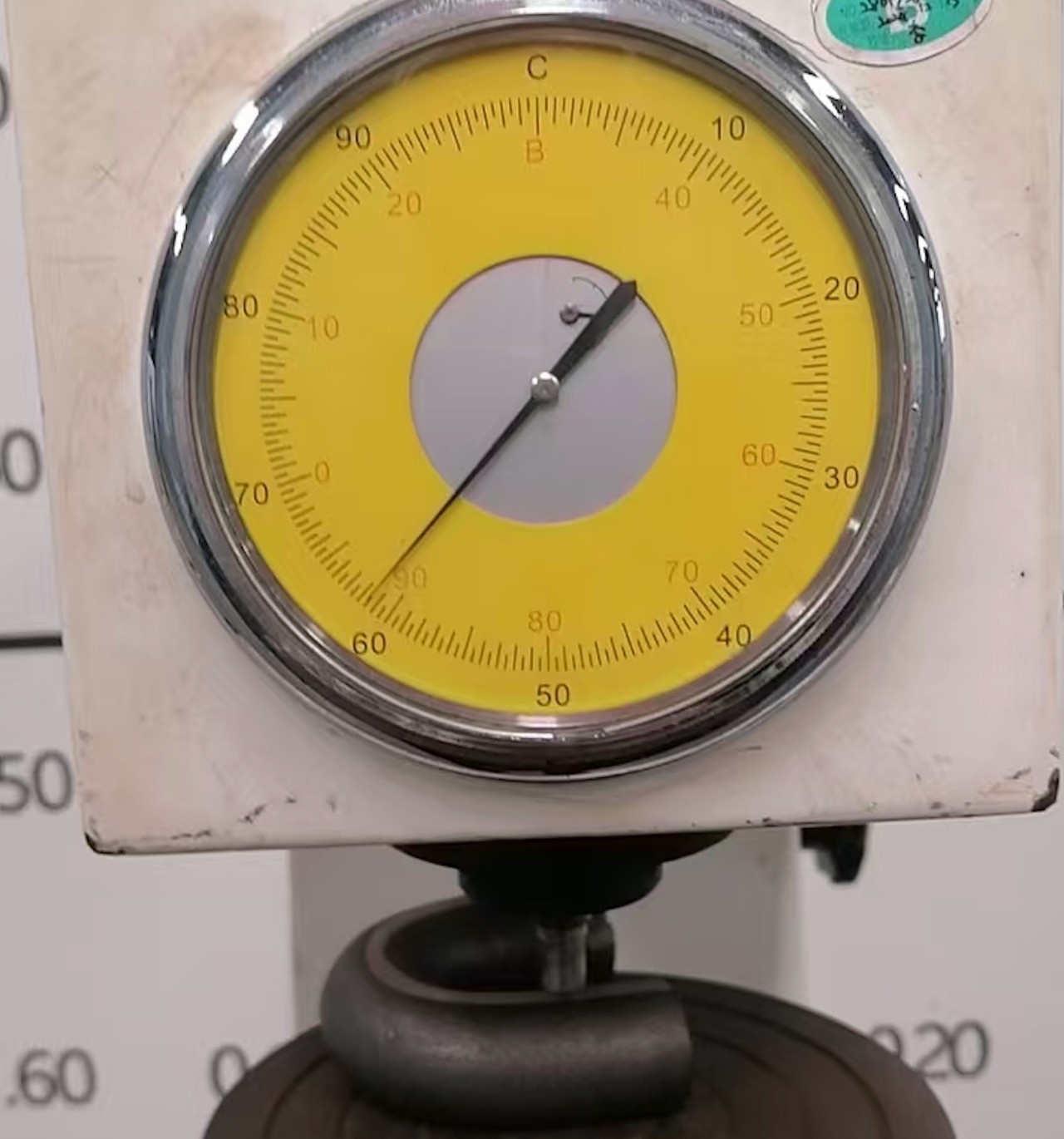
3. Microhardness Test
- Purpose: Measures hardness at a microscopic level, often used to evaluate the hardness profile across the case and core.
- Scale: Vickers (HV) or Knoop (HK).
- Procedure:
- A small indenter is used to make micro-indentations.
- The hardness is calculated based on the indentation size.
- Applications:
- Used to determine the hardness gradient and effective case depth.
- Equipment: Microhardness tester.
4. Brinell Hardness Test (HBW)
- Purpose: Measures hardness of the core material.
- Scale: Brinell hardness (HBW).
- Procedure:
- A tungsten carbide ball is pressed into the material under a specific load.
- The diameter of the indentation is measured and converted to hardness.
- Applications:
- Suitable for measuring core hardness (30–40 HRC equivalent).
- Equipment: Brinell hardness tester.
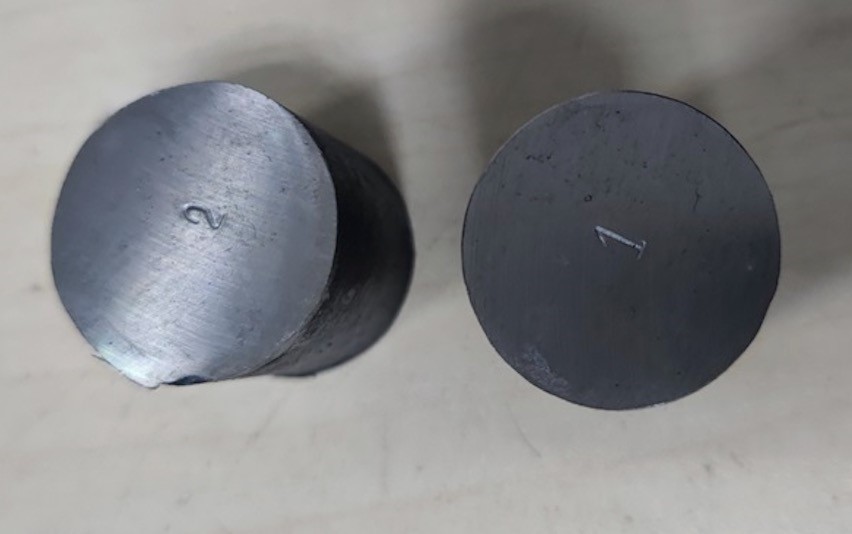
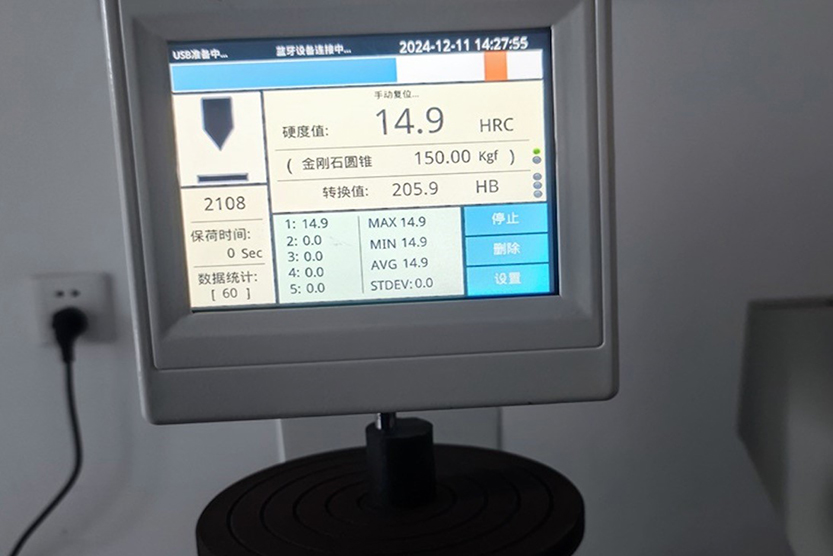
Post time: Feb-04-2025