Master Links and Master Link Assemblies are important components for forming multi-leg lifting slings. Although primarily manufactured as a chain sling component they are used for all types of slings including wire rope slings and webbing slings.
Selecting correct and compatible master links is not straightforward however. There are a good variety of chain sling components we might want to connect while standards and practices vary well – so it is helpful to discuss some of the issues and pointers.
What is Master Link?
Master Links and Master Link Assemblies are also known by other names including oblong links, head rings, multi-master link assemblies etc. They are one of the oldest types of forged lifting tackle and they sit at the apex of multi-leg lifting slings.
Multiple-leg lifting slings can be invaluable for distributing lifting forces and achieving stability and control of a payload we want to lift. The fundamental problem however is that slings and sling components are mostly made for a single connection point to be bearing the load. If we have two, three or four legs to our sling, then each of those legs need something to adapt them to the attachment point (such as a crane hook) or another fitting which accepts only one leg at a time.
Connections
The way that master links achieve connections is important.
For a two leg sling this is fairly simple, the Master Link is rated for up to two sling connections at its lower end:
For a four leg sling, this is also fairly simple. Connecting four loaded legs to the end of the master link is forbidden, but using a Master Link Assembly (Multi-Master Link) we can multiply two by two to get four legs:
Three legs are trickier. Some older documentation may depict three legs into a single link, however, this is now generally forbidden. The proper approach is to use the same method as the four leg arrangement and use only one sling on one of the intermediates.
Two Legged Sling Loadings
Four Legged Sling Loadings
Three Legged Sling Loadings
Working Load Limit
We might look at the pictures above and think life is easy – but not so fast!
What Working Load Limit (WLL) do we need to look for?
This is perhaps the first of many complications we will face.
With a multiple leg sling we must ensure that all of the legs of the sling and the Master Link have sufficient WLL for the job. We can select components in one of two ways – we can choose the legs we need first, then select a Master Link to match – or we can select the Master Link first, then find sling legs with sufficient rated capacities.
To make this calculation we must first know the sling angle.
In Australia this will be the included angle between the sling legs, and the maximum WLL we can assign will be calculated at 60 degrees.
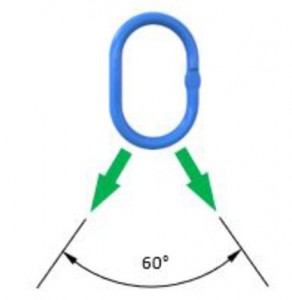
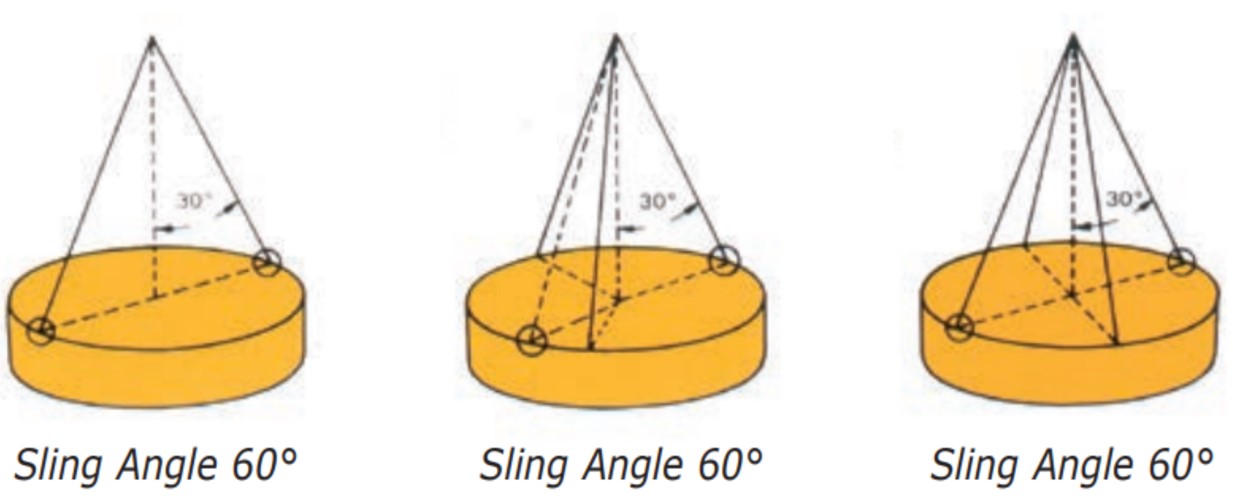
Australian Standard Sling Angle for calculating the maximum WLL.
Having a 60° rating available to us can be very useful because it helps to maximise the potential capacity and usefulness of our slings.
There’s a catch however – and that is the prevalent European standard (EN standard) .
European Standard Chain Sling Angles for calculating maximum WLL.
Here the angle is measured from the vertical, and that isn’t such a problem – but the maximum WLL is calculated at 45° which is an equivalent to Australia’s 90° included angle range. In short, it means that for a given size of chain, the maximum WLL of the sling and that of the compatible master link is smaller.
At an included sling angle of 60°, the master link WLL must be at least 1.73 times the leg WLL.
At an included sling angle of 45°, the master link WLL must be at least 1.41 times the leg WLL.
It also means that product selections and compatibility listed in Europe is not necessarily valid for Australia.
Load Share
Four legged slings form a pyramid. This is convenient because many payloads are rectangular in shape – but it has an inherent problem and that is static indeterminacy. Simply put, the legs don’t share the load evenly.
In fact, there is only one sure bet when it comes to load share and that is to size components as if they share the load on two legs only… that’s what the Australian Standards do – and we can perform tests that show it’s a wise practice.
What it means for our Master link assembly however is that both the upper master link and the lower intermediate links must meet the minimum WLL for the assembly if considered on two legs.
Per AS3775 this means:
Australian Master Link Assembly Requirements.
Again, European rules differ. What they allow is for rating four leg slings on three legs. Of course a four leg sling cannot physically support itself on three legs – it is an approach based purely on numbers.
This is one of those things that sometimes works and sometimes doesn’t. In cases where payloads are rigid and on occasions where the sling proportions come closer to a true pyramidal shape the load share between legs can be quite poor and the sling should be de-rated to account for the resulting slack legs.
What it means for selection of Master Link assemblies however is that when a master link WLL is quoted as a single value overseas – this could mean the intermediate links aren’t strong enough.
A European Master Link works out like this:
This works with EN sling standards, but is not a natural fit with the Australian Standards. Importantly, it simply isn’t as foolproof for the user – that is, unless the product selection has been carefully done to match AS3775 sling rules.
European Standard Master Link Assemblies may need to be de-rated so that the intermediate links are strong enough.
Fitting the Crane Hook
Many sling users face the issue of making slings work with crane hooks. Either the crane hook is too small for the lifting tackle – or the lifting tackle is too small for the crane hook.
For fitting up a masterlink to a crane hook, special caution is urged with combinations that are a tight fit.
All crane hooks are made to be strong in bending in a single plane. To maximise the strength efficiency they use a cross section which is deeper than it is wide, and fatter on the inside than the outside.
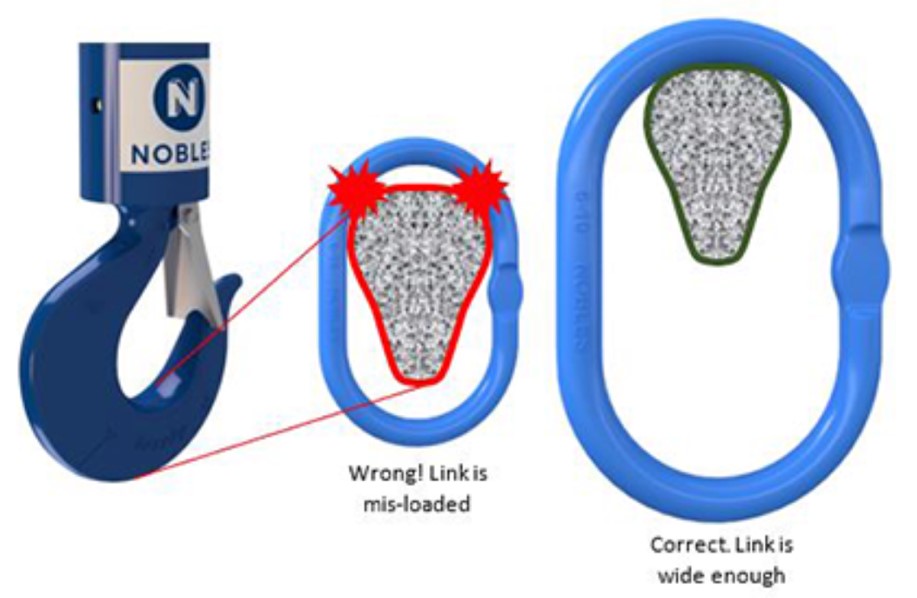
Checking the fit of a Masterlink and hook.
Over-crowding
We need our links to be long enough to fit things like crane hooks at their top as well as fittings at the bottom – but as we see above, often they must be wide enough too.
This is not only a requirement for a crane hook. It is a requirement for the sling leg interfaces.
If the mating parts cannot naturally sit in the link and bear loads correctly the links is over-crowded. This stresses the parts in unusual ways and is not allowed.
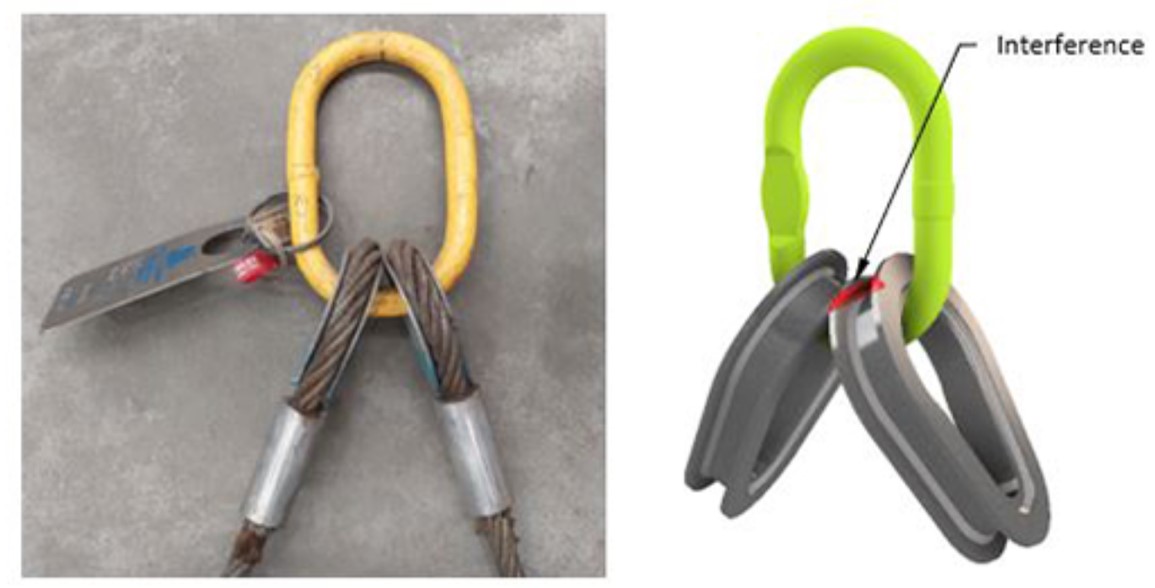
Over-crowding can be a real headache particularly where a masterlink is used with wire rope slings.
In smaller slings finding a good sized link may be easy, but when connections come in larger sizes if it can be overcrowded it won’t work.
In the pictured example the combination of heavy duty fabricated thimbles (right image) interfere with each other and just cannot sit right.
Diameter
Sounds simple – let’s just make links a bit bigger. But having wider links comes at a cost. We still need our links to be strong enough. Within the bounds of available steel strength this invariably means fatter links made with a larger material diameter. This can make it difficult to get connectors to fit.
Many links have a pressed flat to help with engaging a chain connector. It is important to check the mouth dimension of a connector as well as the inside diameter if you want to check whether it fits something like a masterlink or shackle.
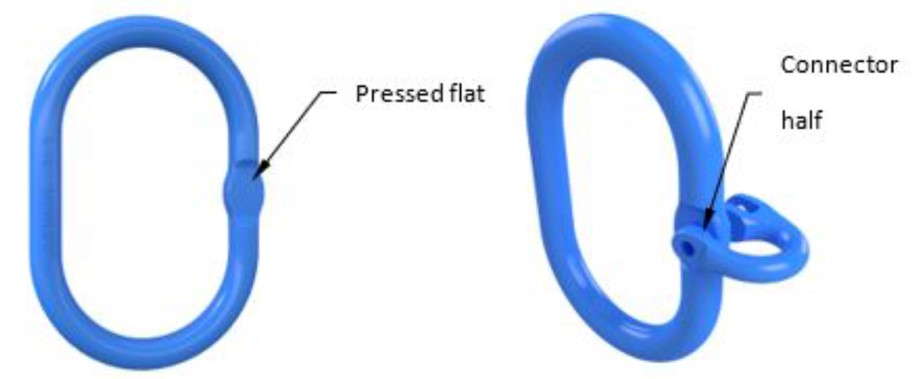
Using a link with a pressed flat to improve compatibility.
Strength
But how strong does a masterlink have to be? Under Australian sling standards the masterlink of any sling* must have a breaking load factor of 4:1 – exactly the same as they do for chain slings.
This is regardless of the breaking load factor of the various sling leg types: Chain, Wire Rope, Round-sling, Webbing, etc. The necessary breaking load factors of the slings, be they 5, 7, or more are preserved so that the different material vulnerabilities are taken into account. These don’t directly affect included chain fittings, so their breaking load factor remains as it was for a chain sling.
This is not necessarily the case in other countries however, and local rules should be obeyed.
* There are some exceptions, the breaking load factor of an entire sling for a personnel carrying crane workbox is doubled, so the link that would be 4:1 is 8:1 when configured for a workbox.
There is more to it of course. Any masterlink must be ductile, it must cope with the normal working life of the sling, and it must survive proof testing.
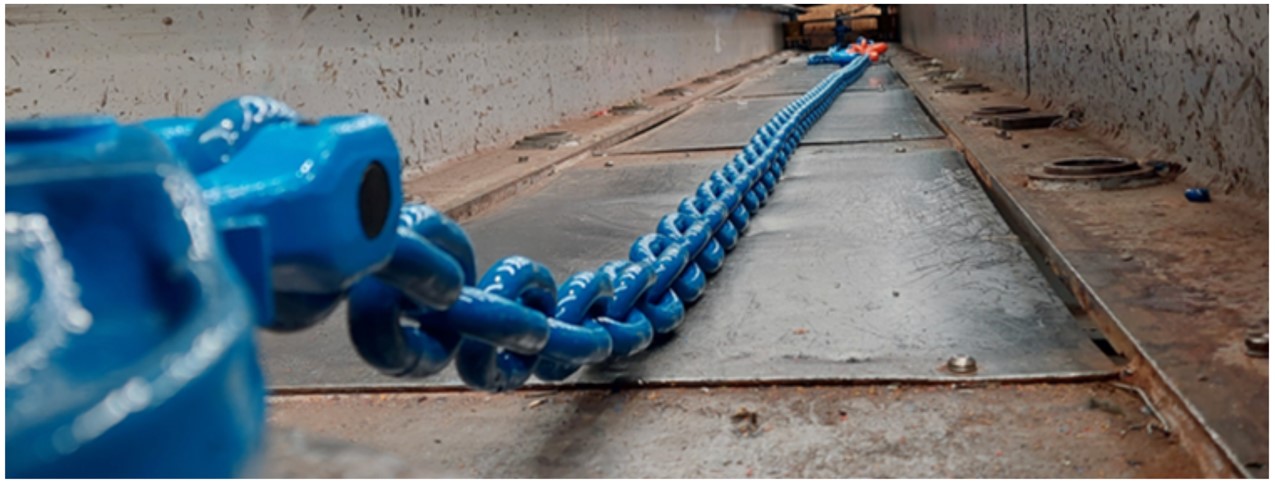
Chain sling with Master Link in the test bed
Importantly – masterlinks are not individually proof loaded until made into a sling that is proof tested. At component supply level masterlinks are only sample tested over mandrels.
Proof testing is an important part of making reliable slings. There is such a variety of parts that fit together that testing provides much needed assurance that all of the parts are strength matched to the tagged WLL – and will survive the rigours of use without deforming.
Testing also protects against component defects.
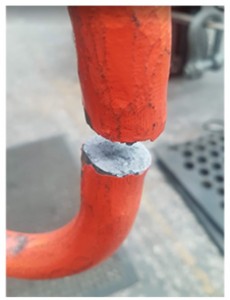
Masterlink with manufacturing defect detected at proof load.
Fundamentals
Fundamentals
Master Links are an essential component when it comes to rigging an overhead lift as they are the connection point for chain slings and the application of other sling types.
Whole books could be written about masterlinks and we are only able to touch upon some of the fundamentals here:
• Master links for multiple leg slings must be correctly configured
• Differences in standards and ratings must be considered when selecting components
• They must fit their correct connections to slings and hooks.
• They must be sufficiently strong.
…and not least, we should look for a matching tag and proof test certificate for masterlinks delivered as part of a sling assembly.
Masterlinks are only as good as their manufacture, use and ongoing inspection.
They must always be selected and assessed by a competent person.
(with courtesy of Nobles)
Post time: Jun-20-2022