I. Importance of Choosing the Right Chains and Shackles
In cement factories, bucket elevators are critical for transporting heavy, abrasive bulk materials such as clinker, limestone, and cement vertically. The round link chains and shackles bear significant mechanical stress, making their design and production quality control essential for operational success. Here’s why selecting the right components matters and how SCIC addresses this:
1. Load-Bearing Capacity: Chains and shackles must withstand high tensile loads and shock impacts from continuous bucket movement. Substandard components risk sudden failure, leading to downtime, safety hazards, and costly repairs. SCIC’s adherence to DIN standards ensures that our products meet the necessary strength requirements, such as the specified breaking force of 280–300 N/mm².
2. Wear Resistance: The abrasive nature of cement materials accelerates wear on elevator components. Case-hardened chains (up to 800 HV) and shackles (up to 600 HV) provide a durable surface to resist abrasion, while maintaining core toughness to prevent cracking. SCIC’s precise carburizing process achieves the requested 10% carburizing thickness and 5–6% effective hardness depth, ensuring long-term performance.
3. Standards Compliance: Compliance with DIN 764, DIN 766, DIN 745, and DIN 5699 guarantees that chains and shackles meet industry benchmarks for dimensions, material properties, and reliability. SCIC’s expertise in meeting these standards ensures consistent quality tailored to heavy-duty applications.
4. Production Quality Control: SCIC’s rigorous quality control—from material selection to final inspection—minimizes defects and ensures dimensional accuracy, hardness, and strength. This capability reduces the likelihood of failures under the harsh conditions of cement factories.
Choosing the right chains and shackles is critical for the efficiency and safety of your bucket elevators. At SCIC, our products are designed and manufactured to meet stringent DIN standards, ensuring they can withstand the heavy loads and abrasive materials common in cement factories. With our rigorous quality control, you can trust that our chains and shackles will provide reliable performance, reducing the risk of unexpected failures and maintenance costs.
II. Balancing Hardness and Strength During Manufacture
Achieving the client-specified surface hardness (800 HV for chains, 600 HV for shackles), carburizing thickness (10% of link diameter), effective hardness depth (550 HV at 5–6% of diameter), and breaking force (280–300 N/mm²) requires a careful balance between hardness and strength. Here’s how SCIC accomplishes this through material selection, heat treatment, and carburizing:
Key Manufacturing Processes
1. Material Selection: High-carbon or alloy steels are chosen for their ability to respond to carburizing and quenching, providing both surface hardness and core toughness.
2. Carburizing: Carburizing diffuses carbon into the steel surface to increase hardness. For a chain link with a 20 mm diameter; Carburizing Depth: 10% of 20 mm = 2 mm; Effective Hardness Depth: 5–6% of 20 mm = 1–1.2 mm at 550 HV; This creates a hard, wear-resistant surface while preserving a ductile core to absorb dynamic loads.
3. Heat Treatment: Quenching: After carburizing, components are quenched to lock in the surface hardness (800 HV for chains, 600 HV for shackles); Tempering: Controlled tempering (e.g., at 200–250°C) adjusts the core’s properties, ensuring toughness and the required breaking force of 280–300 N/mm². Over-tempering reduces hardness, while under-tempering risks brittleness.
4. Balancing Act: Hardness: A high surface hardness resists wear from abrasive materials; Strength: Core toughness prevents brittle fractures under tensile loads. SCIC controls the carburizing depth and tempering parameters to avoid excessive brittleness while meeting client specifications.
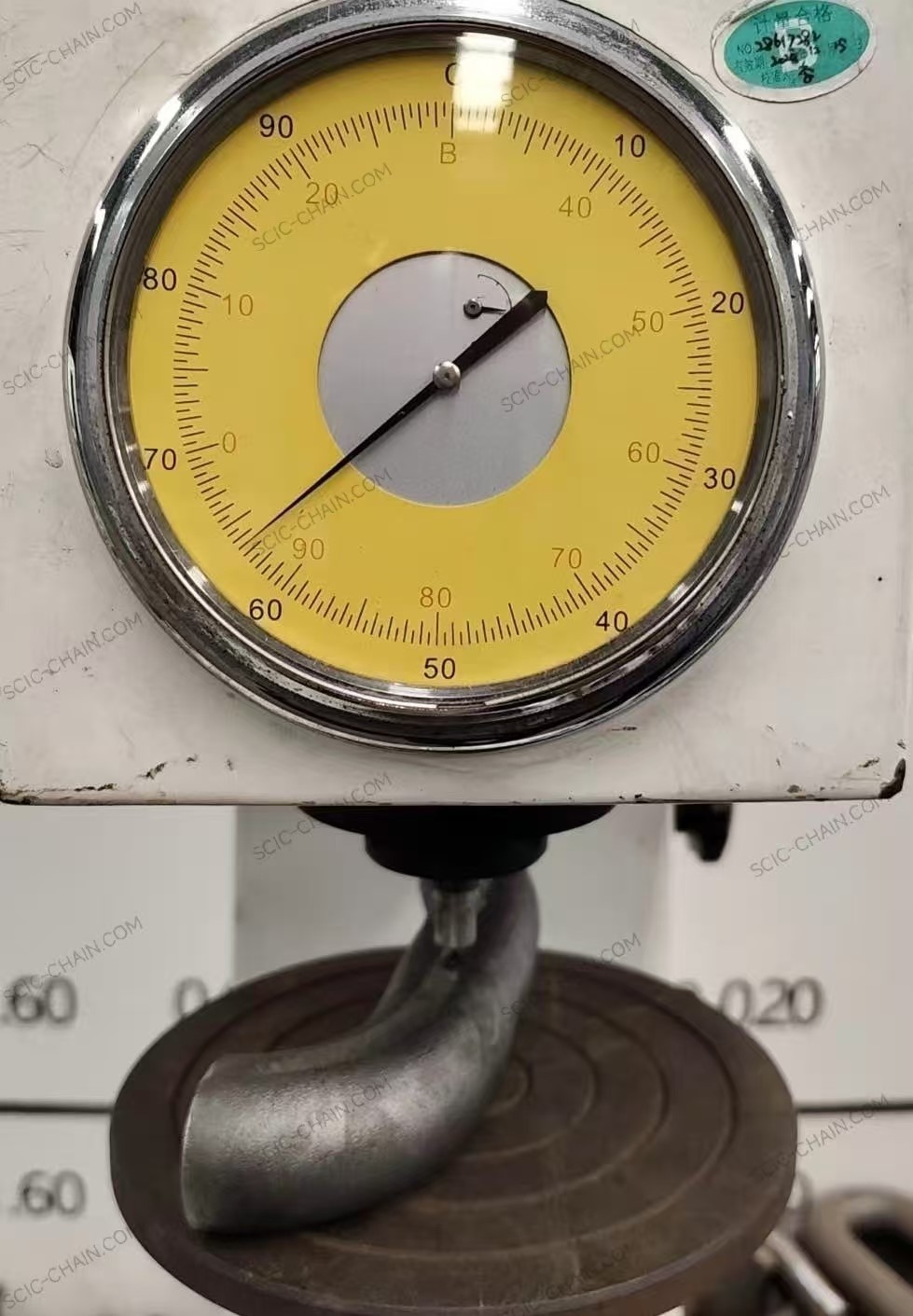
(chain links with high carburized surface hardness)
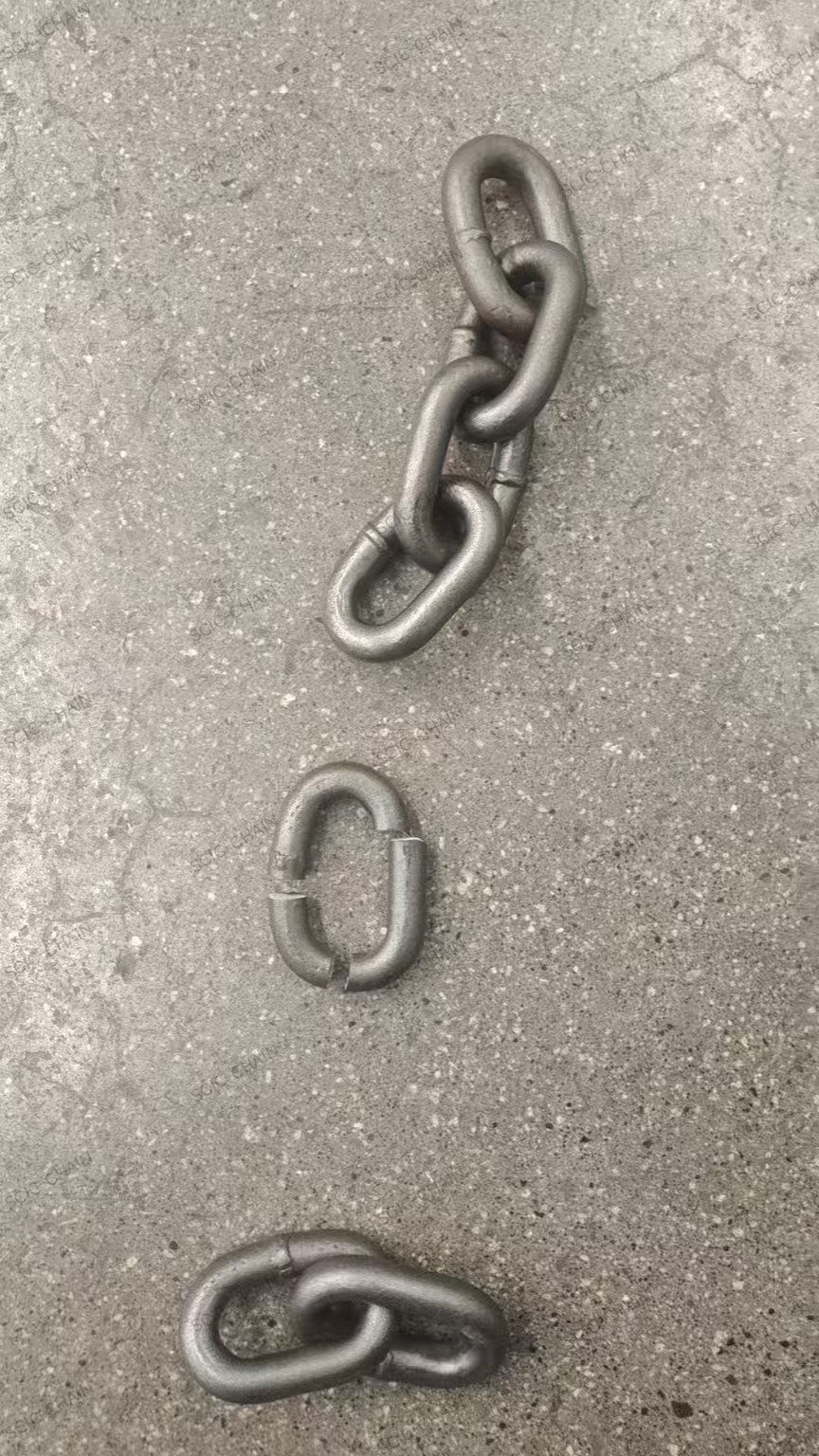
(chain links with high carburized surface hardness, after breaking force test)
Our manufacturing process is meticulously controlled to achieve the perfect balance between hardness and strength. Through precise carburizing and heat treatment, we ensure that our chains and shackles have a hard, wear-resistant surface while maintaining a tough core to handle the dynamic loads in your operations. This balance is crucial for maximizing the lifespan and reliability of the equipment.
III. Ensuring Lifespan Through Operation and Maintenance
Even with high-quality chains and shackles, proper operation and maintenance are vital to maximize lifespan in cement factory bucket elevators. SCIC provides the following guidance to clients:
Maintenance Guidelines
1. Regular Inspections: Check chains and shackles for wear signs, such as elongation (e.g., >2–3% of original length), deformation, or surface cracks. Early detection prevents failures.
2. Lubrication: Apply high-temperature, heavy-duty lubricants to reduce friction and wear. Lubricate every 100–200 operating hours, depending on conditions.
3. Tension Monitoring: Maintain optimal chain tension to avoid excessive slack (causing jerking) or overtightening (increasing wear). Adjust per SCIC’s specifications.
4. Timely Replacement: Replace worn or damaged components immediately to prevent cascading failures. For example, a deformed shackle should be swapped out promptly.
5. Operational Best Practices: Operate within design limits (e.g., avoid overloading beyond the 280–300 N/mm² breaking force capacity) to minimize stress.
To maximize the lifespan of your chains and shackles, follow these practices: regularly inspect for wear, ensure proper lubrication, monitor chain tension, and replace damaged components promptly. By adhering to these guidelines and operating within design limits, you can significantly extend the reliability and efficiency of your bucket elevators.
Case Study: Real-World Impact
Scenario:
A cement factory faced frequent round link chain strands failures, with downtime of 10 hours per month due to chains with only 600 HV hardness and shallow carburizing depth. This led to high repair costs and lost production.
Solution:
The factory adopted SCIC’s case-hardened round link chains:
- Parameters: 30mm diameter, 800 HV surface hardness, 3mm carburizing depth, 1.8mm effective hardness at 550 HV, 290 N/mm² breaking force.
- Maintenance: Bi-weekly inspections, lubrication every 150 hours, and tension adjustments.
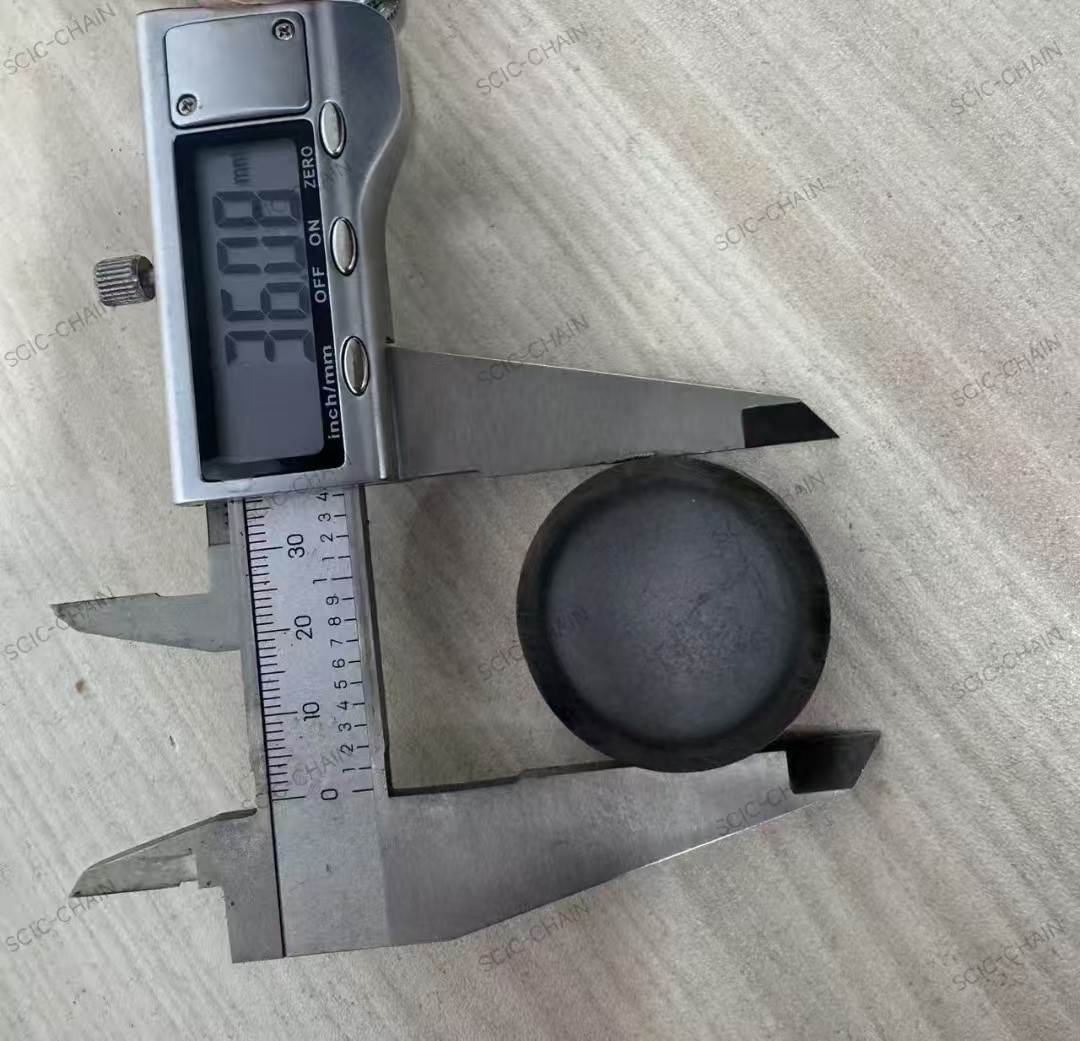
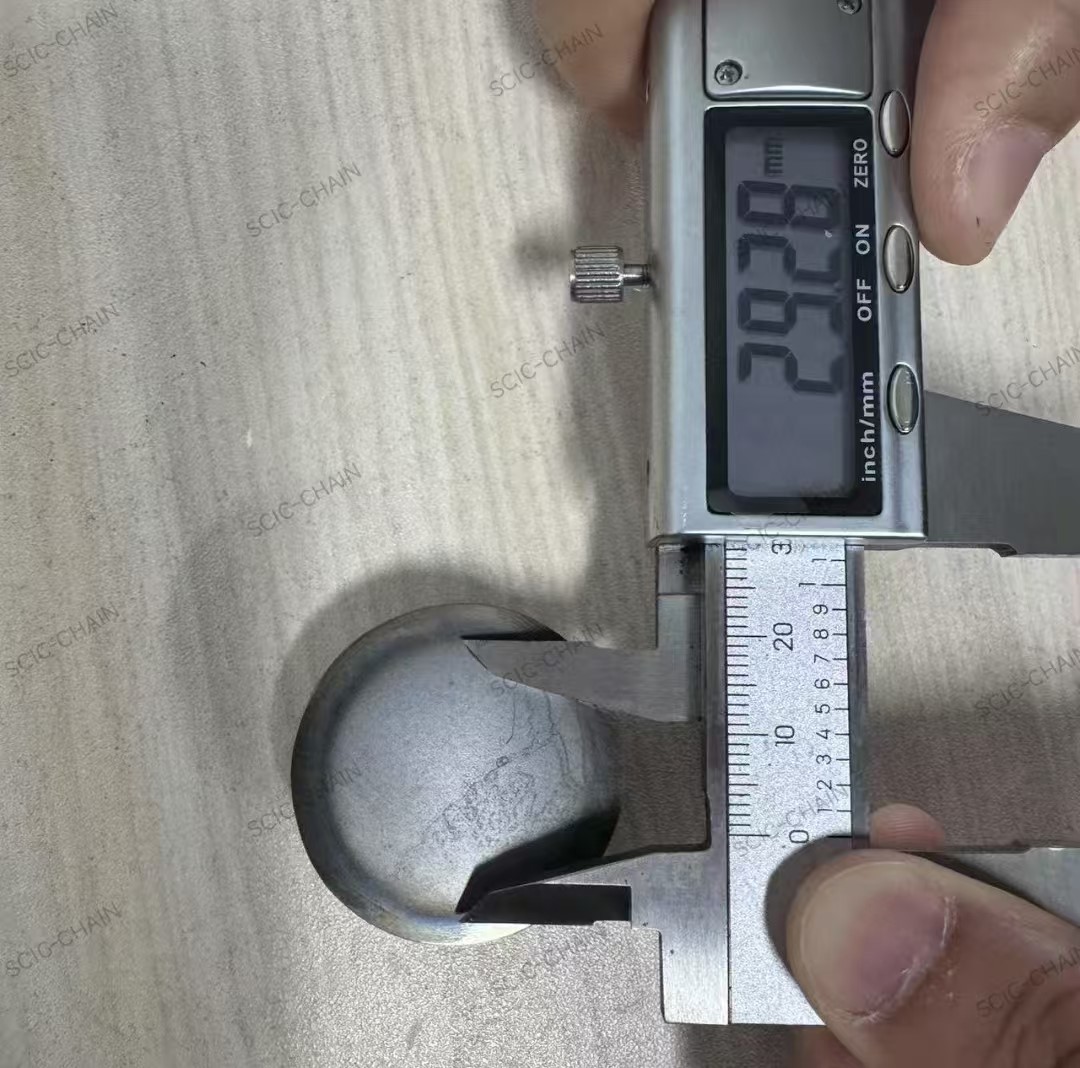
(chain links with improved carburizing depth to 10% link diameter)
IV. Results
1. Downtime: Reduced by 80% (to 2 hours/month).
2. Lifespan: Chains lasted 18 months (vs. 6 months previously).
3. Cost Savings: Maintenance costs dropped by 50% annually.
This demonstrates how SCIC’s high-quality components and maintenance guidance deliver tangible benefits.
V. Conclusion
1. Choosing the Right Components: SCIC’s DIN-compliant chains and shackles, backed by superior design and quality control, ensure safety and efficiency in cement factory bucket elevators.
2. Balancing Hardness and Strength: Our precise manufacturing processes meet client specifications, delivering wear resistance and load-bearing capacity.
3. Maximizing Lifespan: Practical maintenance guidance ensures long-term reliability.
By partnering with SCIC, clients gain access to expertly crafted chains and shackles, tailored to their needs, and supported by proven strategies to enhance performance and reduce costs.
Post time: Apr-21-2025